Energy-saving Renovation of Steam Boiler Systems
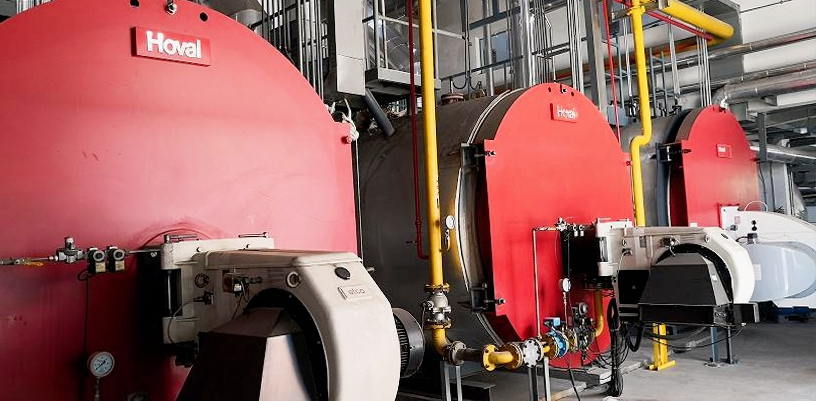
Energy-saving Renovation of Steam Boiler Systems
The energy-saving retrofit of steam boilers is an important measure to improve industrial energy efficiency, reduce operating costs, and decrease environmental impact.
With the growth of global energy demand and the heightened awareness of environmental protection, the energy-saving retrofit of steam boiler systems has become a key to energy conservation and emission reduction in the industrial sector. By adopting advanced energy-saving technologies and equipment, the thermal efficiency of boilers can be significantly improved, leading to a reduction in energy consumption and emissions.
During the operation of steam boilers, heat loss mainly comes from flue gas and surface blowdown. To reduce these losses, we have employed heat recovery equipment from the Hoval brand, achieving effective recovery and reuse of thermal energy. The following example of energy-saving measures for the steam system customized by Hoval for ContiTech illustrates the specific energy-saving effects.
As a subsidiary of Continental, the ContiTech Group is a global expert in the field of rubber and plastic technical products. ContiTech develops, designs, manufactures, and supplies technical products made of rubber and synthetic rubber for use in the automotive and other industries. Hoval provided them with several steam boilers of 8 tons and above, along with their energy-saving systems.
Deaerator Heat Recovery
Deaerators play a role in removing dissolved oxygen in steam boiler systems to prevent corrosion of the boiler and its pipeline system. The exhaust port on the deaerator continuously discharges overflow hot air and steam to the outside, and the loss of this heat energy is considerable. By installing a heat exchange device, we can recover some of the heat for heating the cold softened water entering the deaerator.Taking a 16-ton/hour deaerator as an example, using a heat recovery device can save about 8 cubic meters/hour of natural gas consumption, which not only reduces energy costs but also decreases greenhouse gas emissions.
Surface Blowdown Heat Recovery
During the operation of steam boilers, it is necessary to prevent the chemical concentration in the boiler water from becoming too high, so it is necessary to timely discharge high-concentration high-temperature high-pressure boiler water, i.e., surface blowdown, which contains a large amount of thermal energy.
When the feedwater quality is low, the heat loss from blowdown can even account for 12% of the total input energy. To recover this thermal energy, we have installed heat exchanger tubes in the flash tank of surface blowdown, through which the heat from the blowdown water is transferred to the softened water, thus reducing the loss of thermal energy.
Flue Gas O2+CO Content Control
During boiler operation, to ensure complete combustion, it is necessary to provide an excess of air. However, the excess air heated to high temperatures and discharged through the chimney also causes waste of heat. Therefore, an appropriate excess air coefficient can also improve energy utilization by 0.5-2.0%. In this project, flue gas O2+CO monitoring was set up, and the air intake of the burner was adjusted in time according to the monitoring.
Motor Frequency Conversion
The boiler feedwater pump and the burner fan both have high electrical power and are the main consumers of electricity in the steam boiler system. In this project, both have adopted frequency conversion control technology, and a limited investment will bring long-term energy-saving benefits.
Energy-saving Effect Analysis
Through the application of the above heat recovery technologies, the thermal efficiency of the steam boiler system has been significantly improved. The specific energy-saving effects include but are not limited to:
- Reduced consumption of natural gas, reducing energy costs.
- Reduced greenhouse gas emissions caused by heat loss.
- Increased temperature of boiler feedwater, reducing the thermal load of the boiler, and extending the service life of the equipment.
The energy-saving retrofit of steam boilers not only helps enterprises to improve economic benefits but is also an important measure to respond to the national energy-saving and emission reduction policy and fulfill social responsibility. By adopting advanced heat recovery equipment and energy-saving technologies, energy consumption can be effectively reduced, environmental impact can be lowered, and sustainable development can be achieved.