Poor water quality is harmful to boilers
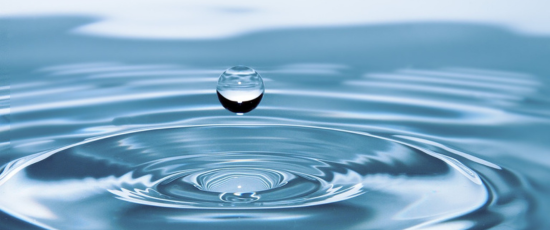
Poor water quality is harmful to boilers
- Blog
- End User
The use of hard and poor quality water, if used as boiler feed water without any treatment, can pose hazards to the boiler operation once it enters the boiler.
Hazard One:
When scaling water is heated and vaporized inside the boiler, it not only provides reaction conditions for impurities in the water but also leads to the continuous concentration of boiler water. When these impurities reach saturation in the boiler water, solid substances precipitate. The precipitated solids, if suspended in the boiler water, are called sludge; if deposited on the heated surface, they are called scale. The thermal conductivity of scale is tens to hundreds of times lower than that of steel. Therefore, when the boiler has scale, it impairs the heat transfer performance of the heated surface. The heat released from fuel combustion cannot be quickly transferred to the boiler water, and a large amount of heat is carried away by flue gas, leading to increased flue gas temperature, increased thermal loss in flue gas, reduced boiler thermal efficiency, fuel waste, damage to the heated surface, reduced boiler output, and scale formation that shortens the service life of the boiler.
Hazard Two:
Corrosion of the boiler's water-cooled walls, convection tube bundles, and drum, etc., can all be caused by poor water quality. As a result, these metal components become thinner and pitted, and even perforated. More severe corrosion can damage the internal structure of the metal. Corroded metal significantly loses its strength. Therefore, it seriously affects the safe operation of the boiler, shortens the service life of the boiler, and causes economic losses. The metal corrosion products carried by the boiler water to the heated surface of the boiler are prone to form scale when combined with other impurities. Scale containing ferric iron is likely to cause iron corrosion of the metal in contact with the scale, and the corrosion products of iron are easy to re-form scale. This is a vicious cycle that can quickly lead to damage to the boiler components.
Hazard Three:
Steam-water surging occurs when the boiler water contains a larger amount of sodium chloride, sodium phosphate, grease, and silicates, or when organic matter in the boiler water undergoes saponification with alkali. During the boiling and evaporation process of the boiler water, foam is produced on the liquid surface. After the foam film bursts and separates, many droplets are released, and these droplets with high salt content are continuously carried away by the steam, resulting in steam-water surging. Steam-water surging in the boiler can cause: severe pollution of steam; salt accumulation in superheater tubes and steam pipelines, which can block the pipeline when severe; a decrease in superheated steam temperature; the liquid level gauge is filled with bubbles, making the liquid level indistinguishable; water hammer effect, which is easy to cause damage to the connections of the steam system; and easy to cause corrosion of the steam valve, return water elbow, and superheater.
Boiler Water Treatment:
So-called boiler water treatment refers to the process of filtering and decomposing water through certain technical treatments to remove impurities and purify it. The purpose is to reduce scale formation, corrosion, and steam-water surging in the boiler, extend the service life of the boiler, save fuel, and ensure the safe and economical operation of the boiler. It can generally be divided into external and internal water treatment. Internal water treatment involves adding a certain amount of chemicals to the boiler to convert scaling substances in the boiler feed water into sludge, which is then removed through blowdown to prevent scale formation in the boiler. This water treatment method is carried out in the boiler, hence it is called internal water treatment.
Advantages of Internal Water Treatment:
1. Internal water treatment does not require complex equipment, so the investment is small, the cost is low, and the operation is convenient.
2. The internal water treatment method is the most basic water treatment method and is a continuation and supplement to external chemical water treatment. After external water treatment, there may still be residual hardness. To prevent scale formation and corrosion in the boiler, certain water treatment chemicals are added.
3. The internal water treatment method does not pollute the environment. Unlike ion exchange and other water treatment methods, it does not discharge the same amount of impurities after treatment and regeneration, along with a large amount of residual regenerant and regeneration by-products. The internal water treatment method turns the main impurities in the water into insoluble sludge, which does not cause pollution to nature. Internal water treatment does not require complex equipment, has a wide range of water quality usage, and is cost-effective and easy to operate. If operated accurately, the effect is good. The internal water treatment method can be used independently for some boilers, and should be used in conjunction with the ion exchange method for some structurally complex boilers. Boiler chemicals are a continuation and supplement to water treatment equipment. Developed countries abroad do this better than our country because they use both methods together. The internal water treatment method has almost no environmental pollution. It is not like ion exchange devices and other water treatment methods, which treat and discharge the same amount of impurities from natural water, along with a large amount of residual regenerant and regeneration by-products. The discharge of regenerants causes soil alkalization. From a macro perspective, the impurities soluble in natural water in nature are not gradually decreasing but gradually increasing. However, internal water treatment mainly turns the impurities in the water into insoluble sludge. Therefore, it does not cause pollution to nature, and the discharged substances are degradable.
Principles for the Use of Chemicals:
1. "Prescribe the right medicine according to the illness" and "tailor-made for different people." Be sure to choose the type of chemical based on the boiler's operating conditions and water quality (water quality test report), that is, use chemicals scientifically according to the "symptoms" of the water quality. First, grasp the first-hand information of the boiler, understand the service time, model, working pressure, water quality, and whether it works continuously or intermittently. Secondly, it is also necessary to understand the scale and corrosion conditions of the boiler, whether the blowdown device is effective, and whether there is a dedicated person in charge.
2. Dose the chemicals according to the actual water usage of the boiler, not according to the boiler's rated output. Overdosing wastes money and increases the salt content in the boiler water; underdosing does not achieve the desired effect. Replenish and dose chemicals in a timely manner to maintain the concentration of the chemicals.
3. Scientific blowdown is necessary to effectively remove the formed sludge from the boiler to prevent the formation of regenerated scale. It is best to guide blowdown according to water quality tests. For boilers that cannot perform water quality tests, strictly follow the blowdown procedures and chemical usage instructions.
4. Strict supervision is required to ensure that the amount of chemicals added is appropriate and the blowdown rate meets the requirements. It is necessary to strictly monitor the quality of the boiler water to guide chemical dosing and blowdown operations. For boilers with scale and corrosion, an inspection should be conducted one month after adding chemicals to check the scale removal and sludge blowdown, providing information and basis for adjusting the chemicals and blowdown rate.